Intelligente Automatisierung für Intralogistikprozesse
Lösungen entlang des Materialflusses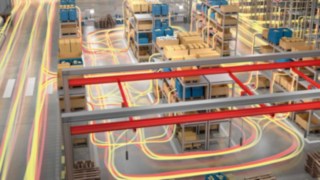
Die moderne Intralogistik steht vor wachsenden Herausforderungen: Onlinehandel und individualisierte Massenfertigung verursachen permanent steigende Stückzahlen und erzwingen immer kleinteiligere Prozesse. Um diese Anforderungen zu bewältigen, sind optimal strukturierte Prozessabläufe unerlässlich. Entscheidend für die Realisierung eines effizienten, unterbrechungsfreien Materialflusses ist ein übergreifendes Verständnis aller intralogistischen Prozesse, vom Wareneingang über die Lagerung und Produktionsversorgung bis hin zum Warenausgang.
Basierend auf einer langjährigen Hardware-Expertise verfügt Linde Material Handling über ein profundes Verständnis aller relevanten Materialflussprozesse. Durch dieses umfassende Prozesswissen ermöglichen wir ganzheitliche Optimierungen, deren Wirksamkeit nicht von der jeweiligen Fahrzeuglösung abhängig ist. Ein entscheidender Faktor der effizienten Prozessgestaltung ist eine intelligente Automatisierung, vom einzelnen Prozessabschnitt bis hin zum kompletten Materialfluss. Die Voraussetzung dafür schaffen wir durch eine kompetente Beratung, die den Ist-Zustand vor Ort präzise analysiert und aus bestehenden Systemkomponenten eine individuell zugeschnittene Lösung entwickelt.
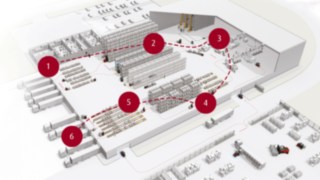
Effizienz in sechs Schritten
Eine moderne Intralogistik lebt von gut strukturierten und akkurat geplanten Materialflüssen. In der Regel umfasst der intralogistische Materialfluss eines Unternehmens sechs separate Prozessschritte, die aufgrund ihrer speziellen Anforderungen unterschiedliche Optimierungsmöglichkeiten bieten.
1. Wareneingang
Jeder innerbetriebliche Materialfluss beginnt mit dem Entladen von Gütern am Wareneingang. Ein falsch geplanter oder schlecht organisierter Wareneingang kann zu erheblichen Störungen im Betriebsablauf führen. Im Wareneingang werden die Waren entladen, geprüft, sortiert, gekennzeichnet und für den weiteren Transport in ein Zwischenlager oder die Produktion vorbereitet. Kurze Durchlaufzeiten, geringer Platzbedarf, minimaler Mitarbeitereinsatz und hohe Prozessqualität sind hier entscheidende Erfolgskriterien.
2. Lagerung
Das Lager ist das Herzstück aller innerbetrieblichen Prozesse. Im Idealfall nutzt es die verfügbare Lagerfläche optimal aus und ermöglicht das effiziente Lagern von Gütern unterschiedlichster Art und Größe. Die Ladeeinheiten müssen dabei schnell und zuverlässig an die vorgesehenen Lager- oder Stellplätze transportiert werden. Kurze Durchlaufzeiten, transparente Abläufe und ein hohes Maß an Flexibilität bei der Einlagerung sind Merkmale einer gut organisierten Lagerhaltung.
3. Produktionsversorgung
Waren und Güter zum richtigen Zeitpunkt an den richtigen Ort zu bringen, ist das A und O einer effizienten Produktionsversorgung. Ob automatisiert oder manuell, die Materialversorgung der Produktion, insbesondere von Montagelinien, lässt sich durch vielfältige Konzepte realisieren, die sich bezüglich Technik, Lagerstufen oder Ablauforganisation unterscheiden. Im Optimalfall entsteht so eine intelligente, gesteuerte und unterbrechungsfreie Warenbewegung mit minimalem Energie- und Kostenaufwand.
4. Kommissionierung
Effiziente Kommissionierungsprozesse haben das Potenzial, die Wettbewerbsfähigkeit eines Unternehmens spürbar zu verbessern. Waren und Güter müssen schnell und effizient aus einem gegebenen Gesamtsortiment zusammengestellt und für eine termingerechte Auslieferung vorbereitet werden. Der Kommissionierungsauftrag wird in Form von analogen oder digitalen Picklisten an den Kommissionierer übermittelt. Der Kommissionierer kann dabei sowohl ein Mensch als auch ein automatisiertes Fahrzeug sein. Um das wirtschaftliche Potenzial der Kommissionierphase optimal zu nutzen, müssen Pickprozesse schnell, präzise und nachvollziehbar sein.
5. Versand
Der Warenversand ist eng mit der Kommissionierung verknüpft. Produkte und Waren müssen durch Konsolidierung zu versandfertigen Einheiten gebündelt werden, um Lagerung und Transport möglichst einheitlich organisieren zu können. Es bieten sich vielfältige Möglichkeiten, diese Prozesse durch Automatisierung effizienter zu gestalten und dabei Transport- und Versandkosten zu reduzieren. Entsprechende Warehouse Management Systeme machen sämtliche Warenflüsse transparent und optimieren deren Steuerbarkeit.
6. Warenausgang
Im Warenausgang werden Waren aus dem Lager bereitgestellt. Nach abschließender Identitäts- und Qualitätskontrolle werden einzelne Packstücke zu einer Sendung zusammengestellt und auf Bereitstellungsflächen positioniert. Gegebenenfalls muss in die Sendungen auch Fremdware unbekannten Inhalts integriert werden. Bereits kleinste Fehler im Warenausgang können ganze Prozessketten ins Stocken bringen. Ein schneller, gut strukturierter und nachvollziehbarer Warenfluss ist in dieser Phase entscheidend.
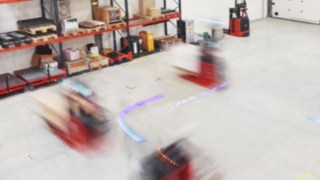
Das nächste Level: Automatisierung
Automatisierung kann ein wichtiger Baustein in der umfassenden Optimierung der innerbetrieblichen Materialflüsse sein. Der Einsatz automatisierter Fahrzeuge bietet sich vor allem dort an, wo simple Transport- und Lageraufgaben permanent wiederholt werden müssen.
Ihre Vorteile im Überblick
Applikationen für Automatisierungslösungen
Automatisierte Fahrzeuge lassen sich auf vielfältige Weise in den Materialfluss integrieren. Je nach Anwendungsbedarf übernehmen sie unterschiedliche Transportaufgaben und sorgen für einen stetigen, unterbrechungsfreien Warenfluss. Ob Transporte von Boden zu Boden, von Boden zu Regal oder von Fördertechnik zu Fördertechnik: Bei standartisierten Applikationen sind automatisierte Lösungen immer ein Gewinn.
Boden zu Boden
Bei automatisierten Boden-zu-Boden-Anwendungen nimmt das Fahrzeug die Ladeeinheit vom Boden auf und stellt sie am Zielort wieder auf dem Boden ab. Die Ladeträger werden zur Aufnahme in definierten Zonen platziert und an festgelegte Zielorte transportiert. Der Vorteil von Boden-zu-Boden-Anwendungen ist, dass außer einem automatisierten Fahrzeug keine weiteren automatisierten Vorrichtungen nötig sind. Daher lassen sie sich in fast allen Phasen des intralogistischen Prozesses integrieren. Sie können Ladeträger vom Wareneingang ins Lager, vom Lager in die Produktion oder aus der Produktion zum Warenausgang transportieren. Wann immer viele Komponenten zur richtigen Zeit auf begrenztem Raum verfügbar sein müssen, sind Boden-zu-Boden-Anwendungen eine gute Wahl.
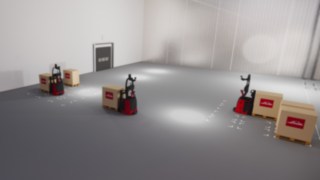
Boden zu Boden - Referenzbeispiel
Bei der Fritz Holter GmbH, einem österreichischen Sanitär- und Heizungsgroßhandel, sind diese ‚magischen Zwei‘ am Werk: Franzl und Gustl, wie die Mitarbeiter sie liebevoll getauft haben. Die beiden fahrenden Transportfahrzeuge der L-MATIC-Serie vom Anbieter für Materialflusslösungen Linde Material Handling arbeiten in zwei Schichten und unterstützen das Kommissionier-Team vor Ort. Der Kommissionierer fordert sie bei Bedarf einfach per Knopfdruck für einen Transport auf der vorgegebenen roten oder grünen Strecke an. Franzl oder Gustl machen sich dann selbstständig auf den Weg zu einem fix definierten Ablageort. Dafür nehmen sie die geforderte rote oder grüne Strecke – tagein, tagaus, ganz ohne komplexe Software. Außerdem musste die Infrastruktur nicht verändert werden, Fußgänger und Fahrzeuge sind nach wie vor auf denselben Strecken unterwegs – unfallfrei, versteht sich. Die Mitarbeiter können sich dank dem unermüdlichen Einsatz von Franzl und Gustl vermehrt auf die Kommissionierung konzentrieren, machen so weniger Fehler und arbeiten insgesamt effizienter. Und die Ware kommt wie von Geisterhand an den gewünschten Zielort.
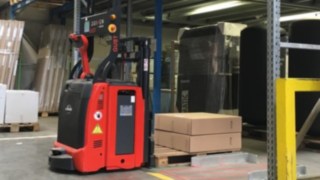
Boden zu Fördertechnik
Boden-zu-Fördertechnik-Anwendungen können in allen Phasen des intralogistischen Prozesses zum Einsatz kommen. Im Wareneingang nehmen automatisierte Fahrzeuge die Ladeeinheiten vom Boden auf und befördern sie in die jeweiligen Lagerbereiche. Dort übergeben sie die Ware an die Fördertechnik des Lagers. Dabei kann es sich um ein vollautomatisiertes Teilelager oder um ein Hochregallager mit automatisierten Schmalgangfahrzeugen handeln. Eine andere häufige Anwendung besteht darin, dass automatisierte Fahrzeuge die fertige Ware nach der Produktion vom Förderband nehmen. Von dort aus bringen sie die Ladeeinheit zur automatischen Palettierung und Wicklung, ins Lager oder direkt zum Warenausgang, um sie dort auf dem Boden abzustellen.

Boden zu Fördertechnik - Referenzbeispiel
Bei großen Warenlagern müssen beladene Paletten oft weite Strecken zurücklegen, um zum Beispiel von ihrem Ablageort zum Förderband zu gelangen. Geschieht dies manuell, ist es häufig mit einem höheren Zeitaufwand und Kosten verbunden. Die Lösung lautet – natürlich: Automatisierung. Bei einem großen Hersteller für papierbasierte Verpackungen in Süddeutschland beispielsweise bringen fahrerlose Transportfahrzeuge (AGV) die Ware zuverlässig und sicher zum richtigen Zeitpunkt von ihrem Ankunftsort an die passende Förderanlage. Das AGV erkennt und positioniert dabei die Ware an der Förderanlage völlig selbstständig. Voraussetzungen hierfür sind einfache Lichtschranken, die an der Fördertechnik installiert sind. Mit ihrer Hilfe kann das AGV dann ganz automatisch die Palette ablegen oder auch wieder aufnehmen, um sie anschließend über eine feste Route wieder quer durchs Lager zu ihrem Zielort zu transportieren.
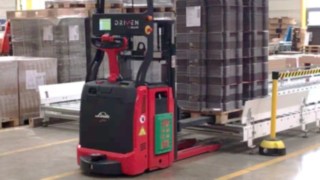
Fördertechnik zu Fördertechnik
Fördertechnik-zu-Fördertechnik-Anwendungen kommen hauptsächlich zum Einsatz, um Ladeeinheiten zwischen stationären Automatiksystemen zu transportieren. Beispielsweise liefern automatisierte Fahrzeuge benötigte Teile vom Ausgang des Automatiklagers zum automatischen Versorgungszugang einer Produktionsmaschine. Nach dem Produktionsvorgang wird die Ware entweder wieder ans Automatiklager übergeben oder zum nächsten Verarbeitungsschritt (bspw. an einer Folienwickelmaschine) transportiert. Anschließend geht die Ware in den Versand. Häufig übergeben automatisierte Fahrzeuge die Ladeeinheiten dort an Gefällebahnen, um sie direkt einem Auslieferungstor oder einem bestimmten Lieferfahrzeug zuzuordnen.
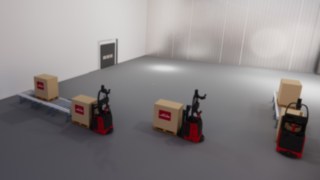
Fördertechnik zu Fördertechnik - Referenzbeispiel
Erhöhte Nachfrage und verdoppelte Produktionszahlen bei unveränderter Infrastruktur – genau hier kommt Automatisierung ins Spiel, so auch bei Massilly France. Der französische Hersteller von Verpackungsmaterialen suchte nach einer Lösung, um seine Waren automatisch zu stapeln und transportsicher zu machen. Und wurde fündig: Ein Linde L-MATIC bringt die Paletten vom automatischen Pallettierroboter zur automatischen Folienwickelmaschine, wartet, bis die Kartons umwickelt sind und verfrachtet sie von dort weiter ins Warenlager. „Die Linde L-MATIC-Lösung ist für uns so spannend, weil sie sich ständig weiterentwickelt und uns nicht zwingt, unsere Infrastruktur zu ändern“, sagt Patrice Ferrero, Produktionsleiter bei Massilly France. Dank einfacher Bedienbarkeit und flexiblen Zwischenladungen lassen sich die AGVs problemlos in die bisherigen Abläufe integrieren und erlauben Massilly France, die Produktion auf Hochtouren laufen zu lassen. Mittlerweile sind jetzt 4 AGVs im Einsatz, weitere Anbindungen sind in Planung.
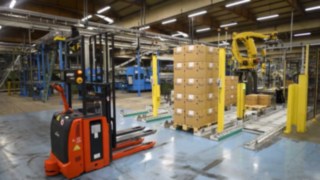
Fördertechnik zu Regal
Fördertechnik-zu-Regal-Anwendungen kommen häufig zum Einsatz, wenn eine Zwischenlagerung der Ladeeinheit erforderlich ist, um eine durchgängige Versorgung von Produktionsmaschinen sicherzustellen. Automatisierte Fahrzeuge transportieren die benötigten Teile vom Regal des Zwischenlagers auf vorgelagerte Förderbänder der Produktionsmaschinen. Anschließend erfolgt der Transport von der Maschine zurück ins Regal. Dort werden die Teile erneut zwischengelagert, bevor sie das Lager verlassen. Fördertechnik-zu-Regal-Anwendungen werden häufig von Automobilzulieferern eingesetzt, um passgenau die getaktete Produktion der Automobilhersteller zu beliefern. In der Verpackungsindustrie wird die fertige Ware von der Fördertechnik der Maschinen in den Versandbereich transportiert, wo sie auf Gefällebahnen oder Regalen für die Abholung bereitgestellt wird.
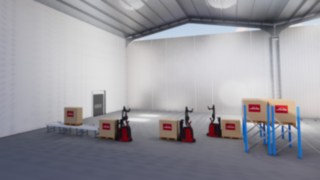
Boden zu Regal
Für Boden-zu-Regal-Anwendungen gibt es unterschiedlichste Einsatzmöglichkeiten. Sie werden häufig im Wareneingang genutzt, um die eingehende Ware in Regalen unterzubringen. Aus dem Lager kann sie anschließend zu Bodenstellplätzen transportiert werden, wo sie von Mitarbeitern abgeholt wird. Boden-zu-Regal-Anwendungen sind besonders flexibel und vielseitig einsetzbar, da keine speziellen Einrichtungen erforderlich sind, um die Ladeeinheiten auf dem Boden zu platzieren. Alternativ kann die Ware für die Zwischenlagerung vom Boden in ein weiteres Regal transportiert werden. Diese Möglichkeit kommt häufig zum Einsatz, um die zeitnahe Versorgung von Produktionsmaschinen zu gewährleisten, selbst wenn das Hauptlager weit vom Verarbeitungsort entfernt ist.
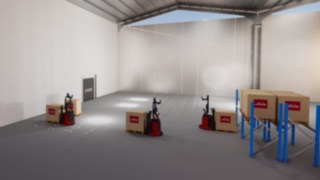